Bosch Introduces New HQL Sterilization Tunnel Series
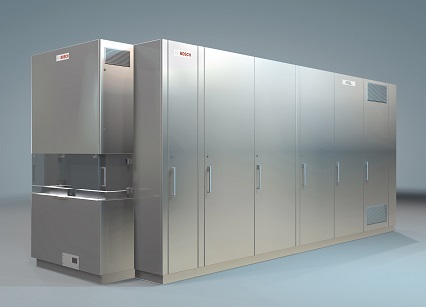
At Interpack 2014, Bosch Packaging Technology, a leading supplier of process and packaging technology, presents the new 6000, 7000 and 8000 series of the HQL drying and sterilization tunnel. This new generation of tunnels is an energy-saving and especially flexible advancement of the proven HQL series for sterilizing and depyrogenizing pre-cleaned ampoules, injection and infusion bottles, as well as cartridges and syringes.
The modular design of the HQL series ensures a customer-specific tunnel arrangement. Each sterilizing and cooling module contains the entire technology for the respective process step. “The modules can now be variably put together. This allows the new series to be flexibly integrated into different line concepts,” Matthias Angelmaier, product manager at Bosch Packaging Technology, explains. In addition, the new design facilitates access to critical areas such as HEPA filters, which can be easily replaced, thus simplifying maintenance of the tunnels.
Savings in Energy and Space
Pharmaceutical manufacturers profit from the increased energy efficiency of the new HQL series. In contrast to most sterilization tunnels, the new series requires less energy for electrical heating and ventilation due to an optimized airflow and measures for heat recovery. A flexible pressure zone concept ensures increased process safety by adapting tunnel pressures in the different zones to customers' requirements. The new tunnels are further characterized by a reduced overall tunnel size, making them shorter and more space-saving than the previous series.
Three Standardized Conveyor Belt Sizes
The new tunnels are available in three standardized bandwidths of 600 respectively 800 mm for the HQL 6000 and 7000 and 1 200 mm for the HQL 8000, which is on display at Interpack. With its different sizes, the drying and sterilization tunnel can be flexibly adapted to different requirements.
“Based on the physical properties of our customers' packaging material we calculate, which tunnel modules are adequate for their processes,” Angelmaier explains. This subsequently facilitates safe process validation and documentation. “The HQL 8000, for instance, with its broad conveyor belt and several sterilizing and cooling modules is suited for large glass containers and downstream filling machines with high output.” The horizontal transport belt made of a stainless steel wire mesh makes sure all freestanding and non-freestanding containers are transported through the HQL tunnel gently and without abrasion.
Related News
-
News Patients vs Pharma – who will the Inflation Reduction Act affect the most?
The Inflation Reduction Act brought in by the Biden administration in 2022 aims to give better and more equitable access to healthcare in the USA. However, pharma companies are now concerned about the other potential costs of such legislation. -
News CPHI Podcast Series: What does the changing US Pharma market mean for industry and patients alike?
In this week's episode of the CPHI Podcast Series Lucy Chard, Digital Editor for CPHI Online is joined by James Manser to discuss the political and market changes in the US pharma field. -
News CPHI Barcelona Annual Report illuminates industry trends for 2024
The CPHI Annual Survey comes into it’s 7th year to report on the predicted trends for 2024. Over 250 pharma executives were asked 35 questions, with their answers informing the industry landscape for the next year, spanning all major pharma marke... -
News Which 10 drugs are open to price negotiation with Medicare in the USA?
The Centres for Medicare & Medicaid Services, under the Biden administration in the USA, has released a list of the 10 drugs that will be open to price negotiations as part of the new legislation under the Inflation Reduction Act (IRA). -
News EU Medical Devices Regulation causes unintended disappearances of medical devices for children, doctors state
Doctor groups and associations have appealed to the EU to correct the EU Medical Devices Regulation law that may cause unintended shortages of essential drug and medical devices for children and rare disease patients. -
News 10 Major Drug Approvals So Far in 2023
Last year, 37 novel drugs were approved by the FDA, this was a high number for such a category, and covered many fields including oncology, demonstrating how promising further research is, and how it is only continuing to build. To date, there are alre... -
News Detecting Alzheimer's disease with a simple lateral flow test
A novel rapid diagnostic test for early-stage Alzheimer's disease has been developed using a biomarker binder from Aptamer Group along with technology from Neuro-Bio, the neurodegenerative disease experts. -
News CPHI Podcast Series: outsourcing and manufacturing trends
Listen to the CPHI Podcast Series this June to hear Gil Roth of the PBOA speak with Digital Editor Lucy Chard about the biggest trends and topics to watch in pharma outsourcing and manufacturing at the minute.
Position your company at the heart of the global Pharma industry with a CPHI Online membership
-
Your products and solutions visible to thousands of visitors within the largest Pharma marketplace
-
Generate high-quality, engaged leads for your business, all year round
-
Promote your business as the industry’s thought-leader by hosting your reports, brochures and videos within your profile
-
Your company’s profile boosted at all participating CPHI events
-
An easy-to-use platform with a detailed dashboard showing your leads and performance