Fluid Bed Dryer
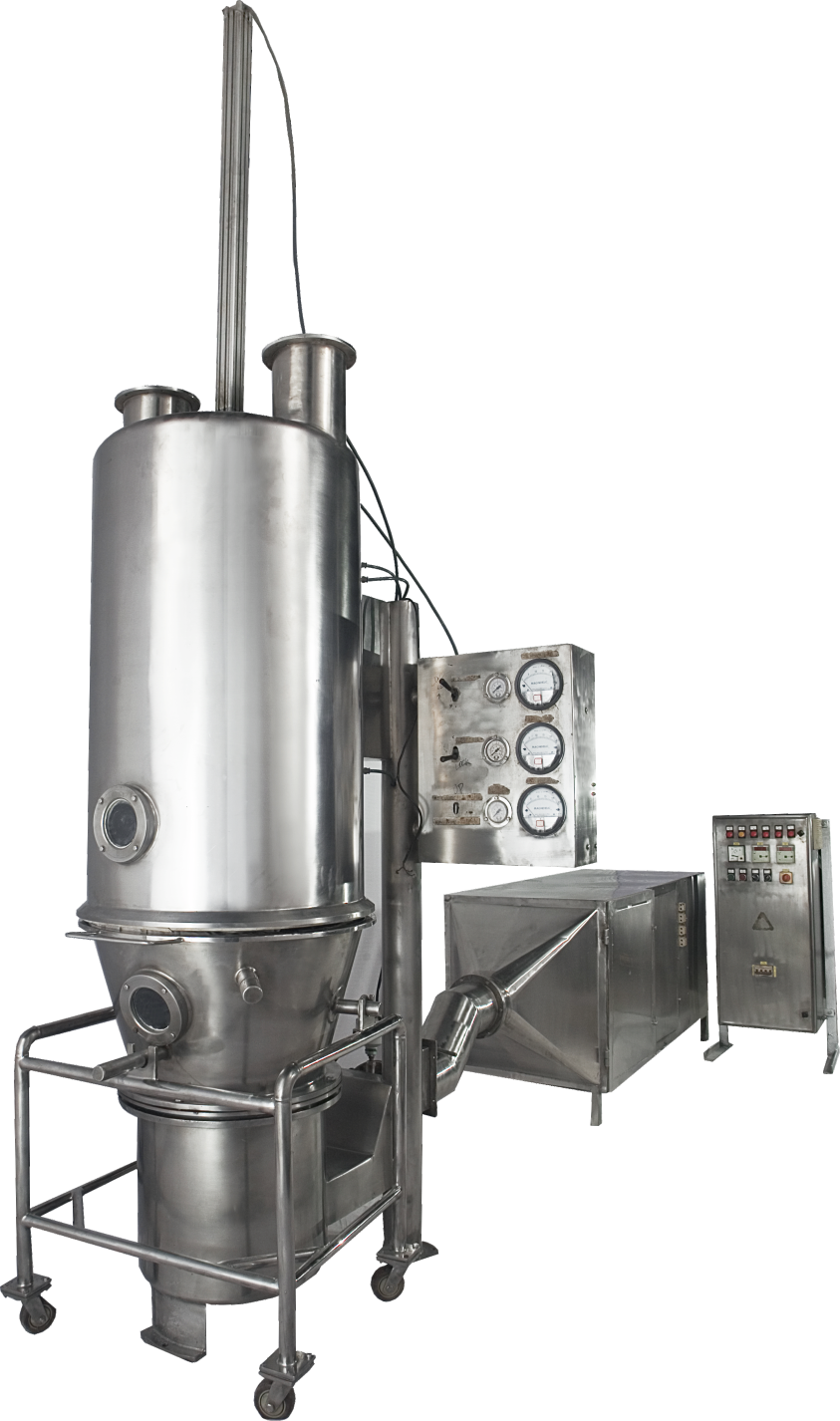
Product Description
Sameto AG Drive Private Limited
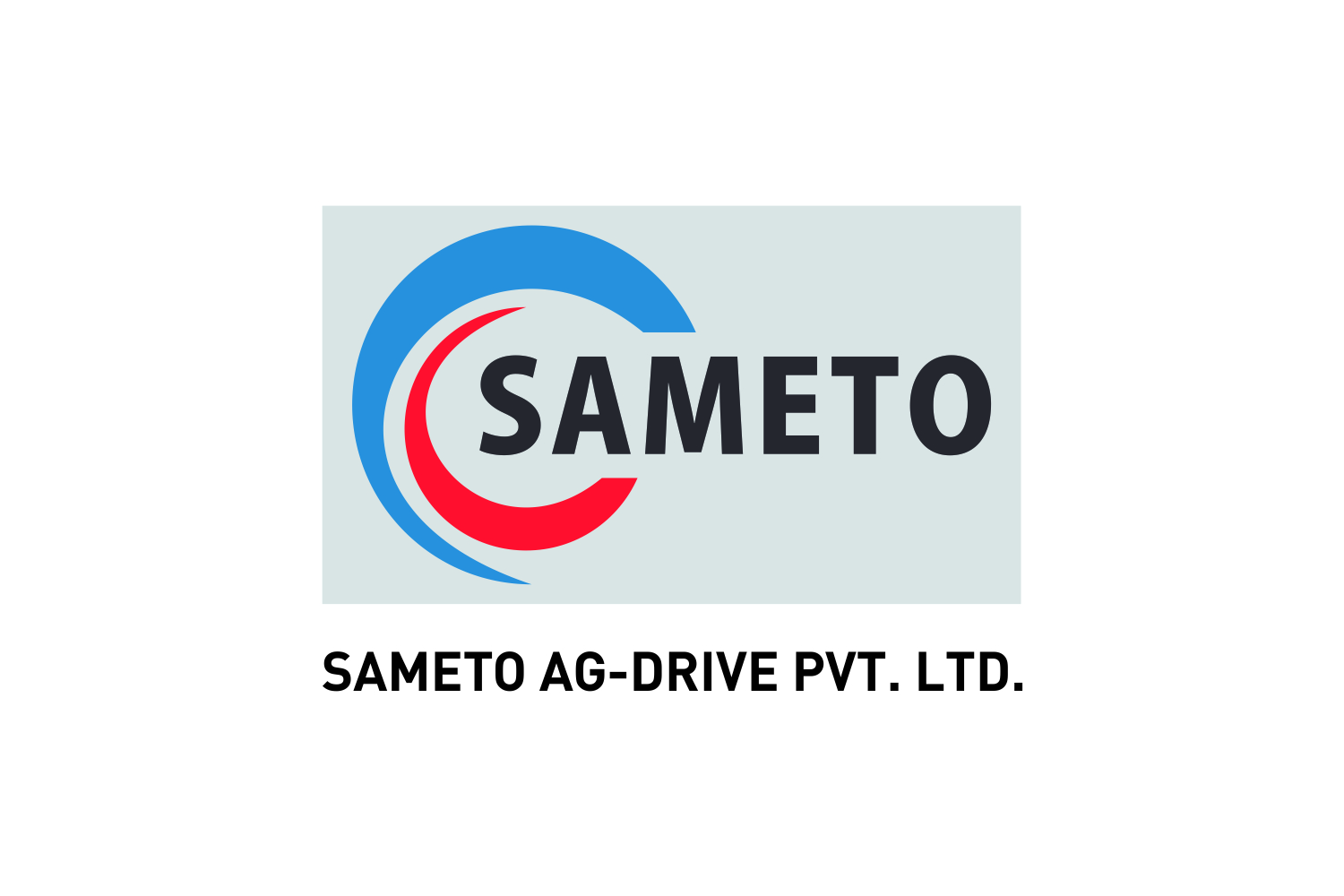
-
IN
-
2019On CPHI since
-
1Certificates
Company types
Categories
Specifications
Sameto AG Drive Private Limited
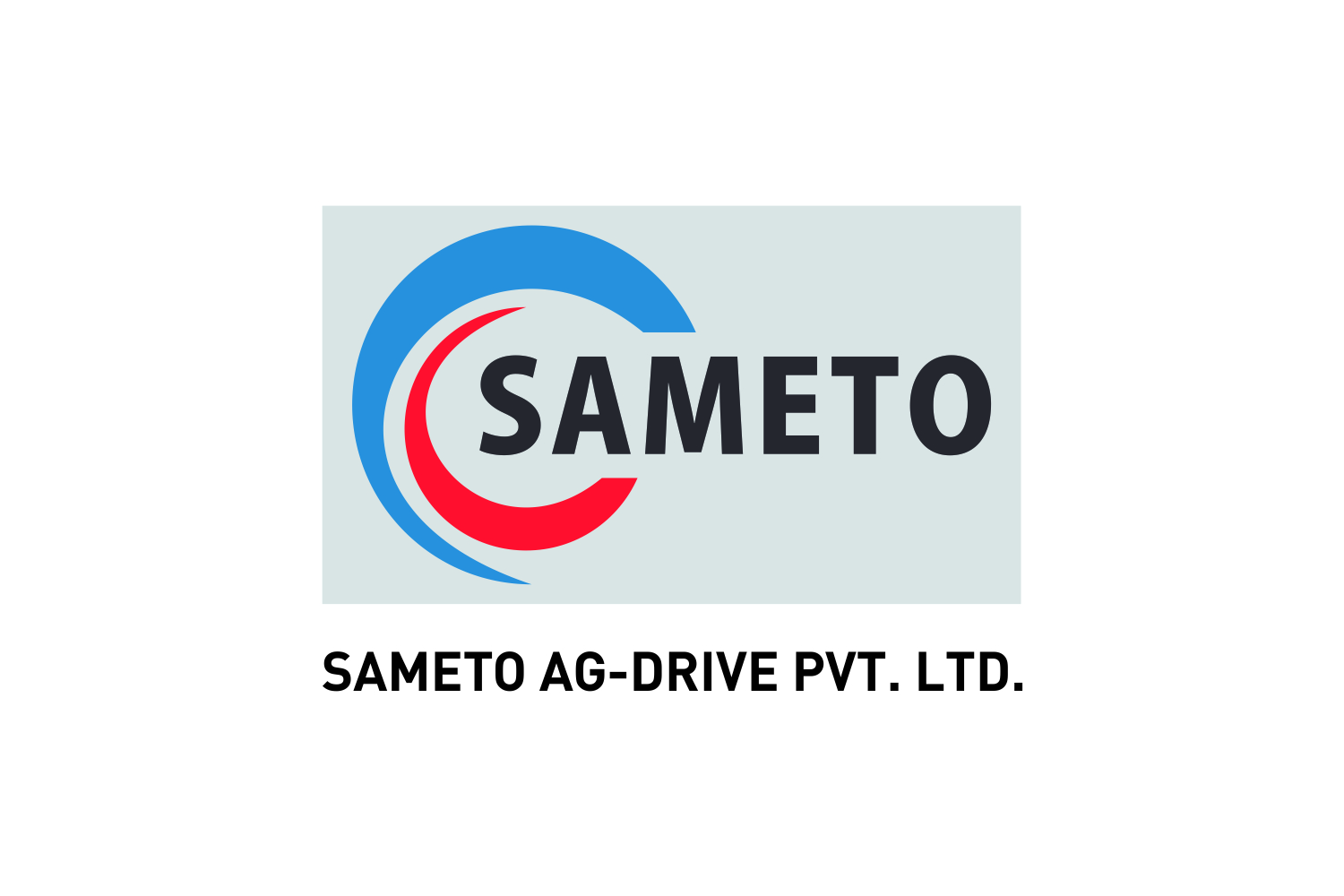
-
IN
-
2019On CPHI since
-
1Certificates
Company types
More Products from Sameto AG Drive Private Limited (2)
-
Product Rapid Mixer Granulation
RAPID MIXER GRANULATOR Machine is used for homogeneous mixing of granulation powder used for production of tablets. It is also used for process of wet mixing & fast dry, humidifying of the powder in Chemical, Cosmetic, Food, Plastic Pharmaceutical, General Mixing Industries, etc.
Rapid Mix... -
Product Double Cone Blender
Double Cone Blenders provide an efficient but gentle blending action. Mixing time will be a bit longer, but mixing efficiency is good .Blending action can be intensive by providing asymmetric cones.(Due to irregular shape.) Optimum performance can be yielded by keeping the internal angle of lower cone ...
Position your company at the heart of the global Pharma industry with a CPHI Online membership
-
Your products and solutions visible to thousands of visitors within the largest Pharma marketplace
-
Generate high-quality, engaged leads for your business, all year round
-
Promote your business as the industry’s thought-leader by hosting your reports, brochures and videos within your profile
-
Your company’s profile boosted at all participating CPHI events
-
An easy-to-use platform with a detailed dashboard showing your leads and performance