Cost-effective, scalable process development of vaccines in cell culture
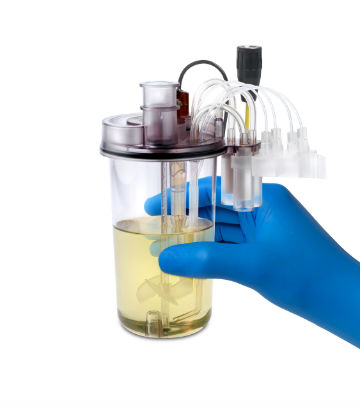
New mini microcarrier bioreactor for ambr high throughput system will enable cost-effective, scalable process development of vaccines in cell culture.
Sartorius Stedim Biotech introduces its mini microcarrier bioreactor for culturing adherent cells.
Sartorius Stedim Biotech (SSB) has launched its new mini bioreactor vessel for its ambr 250 high throughput (ht) system. This new vessel, which is designed for optimal growth of adherent cells on microcarriers will enable rapid, scalable cell culture process development of vaccines. It will be shown on Booth 47 at the BPI European Summit (23-25 April 2018) in Amsterdam, The Netherlands.
The single-use mini bioreactor for microcarrier culture has a working volume of 100-250 mL and features a single Elephant Ear impeller. This impeller type generates optimum mixing and suspension of microcarriers, allowing adherent cells to grow over the entire microcarrier surface. The new mini vessel is based on cell culture bioreactors in the ambr 250 ht system. Utilizing this bioreactor on the ambr 250 ht system will allow rapid scale-up of optimized adherent cell culture processes to SSB’s Biostat STR range of pilot- and manufacturing-scale stirred bioreactors. This results in shorter process development timelines than would be achieved by scientists using benchtop bioreactors and spinner flasks.
Simple to set up and use on the ambr 250 ht, this new single-use mini bioreactor minimizes set-up and turnaround time. With up to 24 bioreactors per ambr 250 ht system, the technology is ideal for Design of Experiments (DoE) studies to optimize process development for vaccine manufacturing using a Quality by Design (QbD) approach.
The new vessel has been tested in collaboration with bioprocess experts at Aston University and University College London as part of an Innovate UK funded project. During these studies, all the cell culture parameters were controlled by the ambr 250 ht automated workstation. The results showed that the new microcarrier vessel design enabled growth to confluence of Vero cells on Cytodex microcarriers’ surface.
“There has been increasing interest in using microcarriers for culturing adherent cell lines in single-use stirred bioreactors as they offer a cost-effective alternative to two-dimensional approaches for vaccine production using T-flasks and roller bottles,” stated Dr Barney Zoro, ambr Product Manager at Sartorius Stedim Biotech. “We are proud to be introducing our new ambr 250 mini bioreactor for culturing adherent cells at the BPI European Summit. Scientists visiting us on Booth 47 will find out how they can use our new mini bioreactor as a predictive model to help shorten their process development timelines and reduce their vaccine manufacturing costs.”
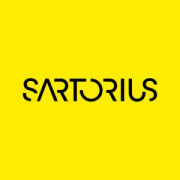
Related News
-
News Eli Lilly’s Alzheimer’s drug receives approval from US FDA
After facing several hurdles on its path to approval last year, Eli Lilly’s donanemab treatment for early Alzheimer’s, brand name Kisunla, received US FDA approval this past week. It is the second therapy for slowing the progression of Alzh... -
News This week in GLP-1 drug headlines: Manufacturing investment and new market launches
As drugmakers race to put their own GLP-1 drug products forward as the next biggest thing in weight-loss, current products are making numerous headlines this week with a number of new developments in their commercialisation and approval. Discover the l... -
News Women in Pharma: Regulating equity across regional borders
In our monthly series focusing on women in the pharmaceutical industry, we interview leading experts in the pharmaceutical supply and value chain to discuss the importance of gender diversity in healthcare, the workplace, and beyond. -
News Viral marketing for B2B pharma businesses: a CPHI Online case study
Discover how a Chinese chemical manufacturing company went viral on TikTok, and what their viral success means for the future of B2B digital marketing for the wider pharmaceutical industry and supply chain. -
News New Aurigene biologics facility opens in Hyderabad, India
Aurigene Pharmaceutical Services Ltd. have opened a biologics facility in Hyderabad, India in a biocluster known as Genome Valley. -
News Novo Nordisk launches 'Power of Wegovy' national campaign
Danish drugmaker Novo Nordisk have launched a new national campaign – The Power of Wegovy – that aims to educate those living with obesity on their blockbuster drug Wegovy throughout the United States. -
News Women in Pharma Anniversary: Celebrating Our Heroines of Pharma
Our Women in Pharma interview series is approaching its 1-year anniversary this month, and to celebrate, we are highlighting the Heroines of Pharma that our very own Women in Pharma admire. -
News Sanofi gains rare disease therapy in acquisition of Inhibrx for US$1.7 billion
Sanofi completed the acquisition of the clinical-stage biotech company Inhibrx in late May 2024 after settling on a US$1.7 billion buyout. The acquisition brings with it a rare disease therapy to bollster Sanofi's pipeline.
Position your company at the heart of the global Pharma industry with a CPHI Online membership
-
Your products and solutions visible to thousands of visitors within the largest Pharma marketplace
-
Generate high-quality, engaged leads for your business, all year round
-
Promote your business as the industry’s thought-leader by hosting your reports, brochures and videos within your profile
-
Your company’s profile boosted at all participating CPHI events
-
An easy-to-use platform with a detailed dashboard showing your leads and performance