Sanner invests in Bensheim production facility
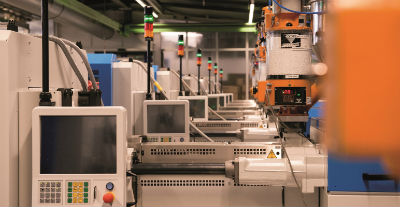
14 new injection-molding machines of the latest generation make Sanner’s production in Bensheim ready for the future.
14 new injection-molding machines and significant increase in efficiency and energy savings.
Sanner has successfully completed the expansion of its production facility in Bensheim. Fourteen new, state-of-the-art injection-molding machines were installed to improve production processes. With an investment of close to 3 million euro, Sanner has paved the way for future-oriented manufacturing at its headquarters.
One year after its start, Sanner has successfully completed the “future project production area South”. During the project, the entire machine park in this area was replaced with 14 injection-molding machines of the latest generation. The Sanner team completed the project on schedule and within the designated budget. “Our goal was to further automatize production and consequently increase capacities and efficiency,” says Dirk Mähr, Managing Director of Sanner GmbH. “A goal we have definitely achieved.”
Ready for industry 4.0
With this expansion, the company is taking another important step towards future-oriented production at its headquarters in Bensheim. The new injection-molding machines ensure faster processes and can be further automatized at any time. The packaging specialist is thus optimally equipped for the challenges of industry 4.0, as well as for further optimization projects. Over the next few years, Sanner will also consequently expand its portfolio in the areas of capsules and desiccant packaging.
Focus on sustainability
“During the modification, we were also able to significantly reduce energy consumption in production in line with the Sanner sustainability concept,” Mähr adds. This includes, amongst others, a renewed media supply for cooling water and compressed air, a better raw material supply and the installation of new cranes. Thanks to new lighting and a reduced noise level, Sanner employees also benefit from easier workflows and better working conditions.
Related News
-
News US BIOSECURE Act passed by US House of Representatives
The controversial act, which has already impacted several foreign companies operating in the US, was passed by the House of Representatives on September 9, 2024. It is now headed for the US Senate before it can be signed into law by President Joe Biden... -
News Pharma Supply Chain People Moves
The latest appointments, promotions, and structural changes across the pharmaceutical supply chain. -
News Drug prices agreed upon as part of the US Inflation Reduction Act
The Inflation Reduction Act brought into constitution by the Biden administation in 2022, which proposed a drug price negotiation between the government and pharmaceutical companies, has reached it's first agreement. -
News BIOSECURE Act continues to loom over Chinese pharma manufacturers
With the US BIOSECURE Act on its way to passing into legislation, Chinese companies are facing declining revenues within the first half of 2024 as US pharmaceutical and healthcare companies pull their businesses from the country. -
News Ophthalmologic drug product Eylea faces biosimilar threats after FDA approvals
Regeneron Pharmaceutical’s blockbuster ophthalmology drug Eylea is facing biosimilar competition as the US FDA approves Biocon’s Yesafili and Samsung Bioepis/Biogen’s Opuviz. -
News ONO Pharmaceutical expands oncology portfolio with acquisition of Deciphera
ONO Pharmaceutical, out of Japan, is in the process of acquiring cancer-therapy maker Deciphera Pharmaceuticals for US$2.4 billion. -
News First offers for pharma from Medicare drug price negotiations
Ten high-cost drugs from various pharma manufacturers are in pricing negotiations in a first-ever for the US Medicare program. President Biden’s administration stated they have responded to the first round of offers. -
News Eli Lilly’s Zepbound makes leaps and bounds in weight-loss drug market
In the last week, Eli Lilly has announced their partnership with Amazon.com’s pharmacy unit to deliver prescriptions of Zepbound. Zepbound has also surpassed Novo Nordisk’s Wegovy for the number of prescriptions for the week of March 8.&nbs...
Position your company at the heart of the global Pharma industry with a CPHI Online membership
-
Your products and solutions visible to thousands of visitors within the largest Pharma marketplace
-
Generate high-quality, engaged leads for your business, all year round
-
Promote your business as the industry’s thought-leader by hosting your reports, brochures and videos within your profile
-
Your company’s profile boosted at all participating CPHI events
-
An easy-to-use platform with a detailed dashboard showing your leads and performance