Bormioli Pharma set out ambitious 50-in-5 sustainability targets
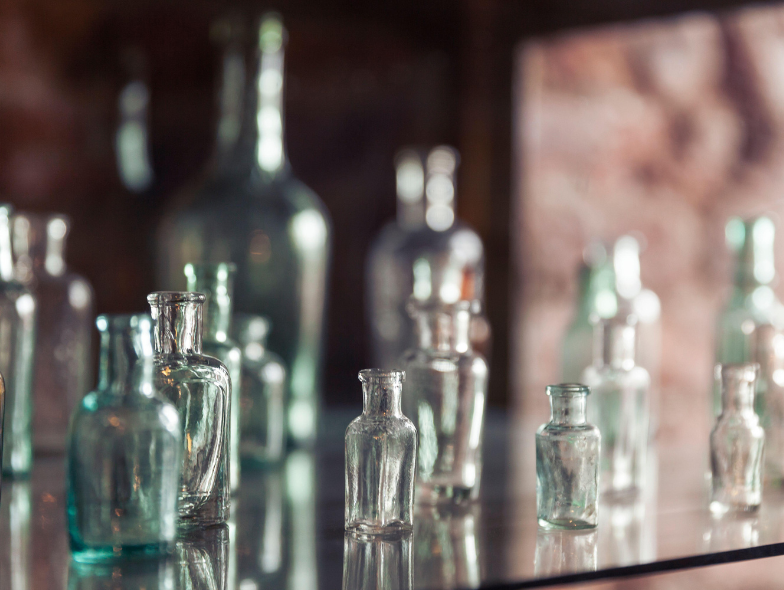
Bormioli Pharma has been designing innovative packaging solutions for the pharmaceutical industry for 200 years; in this interview Andrea Sentimenti described how they keep current in today's pharmaceutical landscape and how they are implementing sustainable initiatives.
Please could you introduce yourself and your role at Bormioli Pharma?
My name is Andrea Sentimenti and I am the Marketing & Innovation Director at Bormioli Pharma, a group of companies that designs and produces innovative glass and plastic primary packaging solutions for the pharmaceutical industry. I’ve been a member of the senior leadership team for 3 years and I'm running the marketing innovation department globally. In the marketing department, our main function is investigating and understanding what are the needs of our customers and transforming those needs into ideas and then into the form of final solutions or products. We are proud to say that we are connecting the dots between the needs of the market and our ability to fulfil those needs and wants. Our team has quite a broad range of experience and competencies so we can merge technology, product design, business knowledge, and market acumen to serve customers.
We are doing this end-to-end project and portfolio management for all the product ranges for Bormioli Pharma, and of course innovation and sustainability are fundamental to that. We like to say innovation is in our DNA, after all, we were the first to develop a pharmaceutical-grade glass container almost one century ago. Then we were among the first to introduce moulded borosilicate glass in pharma – the golden standard for pharmaceutical application. Bormioli Pharma has always been a pioneering company and a company that is always working towards changing the status of the pharmaceutical packaging industry.
In 2019, we decided to implement an innovation program that we named Bormioli Pharma Invents with a view to move forward from packaging to packaging solutions and then from packaging solutions to medical devices, taking advantage and leveraging the new technologies that are currently available on the market.
Bormioli has been running for nearly 200 years. Can you explain the drivers behind how you continue to innovate as a leader in the packaging industry?
Yes, we have a very specific innovation business model that we developed in the past few decades and we have been strengthening that over time. While we are securing short-term incremental innovation needs, we are investigating the unmet needs and wants of our customers and the needs of their customers, who are the patients. In fact, our market research team surveys patients and healthcare professionals to understand how they would improve packaging, or the main pain points in taking their prescriptions. These findings are used to start crafting and developing innovative solutions to address these needs.
Thanks to that research-based, stakeholder-focused methodology, in recent years, we already have 4 patents granted and many others pending. In total, something like 12 patents will be part of our offering in the following years.
Innovation is value. We want to generate value for our customers through the fact that we are creating solutions for their customers. So that's what keeps us a little bit ahead of the competition, even after 200 years of brilliant history.
Leading up to your 200-year anniversary in 2025 you’ve launched a 50-in-5 programme, can you please explain what this entails?
Sustainability has been one of the main targets at Bormioli for decades, from a time when it wasn’t so ‘mainstream’. Thanks to that, we have developed an established range of solutions.
Using recycled or sustainable materials is something that is quite common right now, but it's not so common as to fit the very stringent use and safety requirements of the pharmaceutical industry. What we did was to develop sustainable solutions matching exactly the needs of the pharmaceutical industry based on experience from successes we have had in the past few years.
The idea was that we really want to follow our vision and our mission to provide healthcare solutions, but solutions that are not just good for the patient or for the user, but also kind to the planet in which we live. We must have some commitments for our planet, so we decided that in five years we would achieve 50% of sustainable or recyclable materials in our production line and that's why we initiated this 50-in-5 programme. It's a program that is already providing good results.
The 50-in-5 programme that we are deploying right now is offering a solid sustainable solution to the pharmaceutical industry, well in advance compared with the limit stipulated by the European Union’s single plastic use directive that is requiring by 2035 a minimum of 30% of recycled materials. We want to be able to offer to the pharma industry sustainable packaging solutions in almost any kind of packaging form they need. Supporting a sustainable growth business model, caring for the patient and for the planet; this is what we call Bormioli Pharma’s EcoPositive attitude.
In order to offer a supply chain that is sustainable from the packaging perspective, we are working on many different topics including recyclability of glass, increasing the amount of recycled glass based on the limits and rules from the international pharmacopoeia. For example, we are probably the first company offering the pharmaceutical industry recyclable PET pharma-grade products. Here we are not referring to a sampling, but to real mass production and these products are already on the market. Then we have bio-based solutions, in the form of products obtained from renewable material such as sugar cane. We have PLA-based products of polylactic acid coming from waste of corn. We have recycled polypropylene; we have recycled HDPE; we are offering the possibility for a pharmaceutical company to get a package that is in full or partially sustainable. So using a limited amount of non-renewable sources and that goes a long way in the direction of the directives that the European Union is trying to implement right now.
Which key areas are you investing in to help you meet your target?
The recyclability of glass is probably one of the most important parts that we are investing in right now. We know that making glass is a carbon-intensive manufacturing process. You have to melt the glass up to 1600 °C. So that requires a lot of heat. What we are doing is we are improving our processes in terms of technologies. But we are also increasing, step-by-step, the amount of recycling and recycled glass collected from a controlled supply chain in order to reduce the amount of ‘virgin’ glass. For those kinds of products, where we are allowed to do it, we are remelting glass that municipalities are collecting through post-user consumption.
There are regulations on the use of such glass; for example, in Type 1 borosilicate glass, it is prohibited by law to use recycled glass. But for areas where a certain percentage of recycled glass is acceptable, we are trying to make our process as efficient as possible. In this instance, we are collecting scrap glass from our manufacturing processes, and because it has not exited our facility, it is permitted by law to be re-used.
We are therefore using 100% of the glass where it is reused in our production, avoiding any kind of waste, and that goes for glass together with some big investments in terms of improving the efficiencies of our melting furnaces on plastic.
Plastic right now does not have a very good reputation in terms of sustainability, but we know that it is a great product of many uses and is also recyclable. We started with PET because PET has a very straightforward supply chain and recycle system; we are using only recycled PET from bottled water. With recycled PET that has not been contaminated in any way by other products, we have been the first one to offer recycled PET bottles and containers that are pharma-grade and meet the International Pharmacopeia requirements.
Then we have a bio-based and recycled HDPE, which is the preferred materials for containers for pills and tablets. Also in this case, we are sourcing recycled HDPE from a very specific and safe supply chain (post-consumer milk bottles only) so it is a very safe and consistent product.
We have in our product range also a “carbon capture PET solution.” This is a polymer generated by using as a primary component, carbon dioxide captured from the environment, whereby the product is not generating any kind of CO2 but through a very innovative process contributes to reducing the amount of this global warming gas. CO2 collected is then transformed through fermentation into materials (MEG) used for production of PET, and that's something that we have already available on the market.
For our aluminium seals, a key product for precious parenteral and injectable applications, we are introducing recycled aluminium.
So everything has been designed and organised to minimise the environmental impact. But that's just a part of the ethos for the 50-in-5 programme. Having the right technologies and the proper technological solutions is fundamental and it is mandatory to deliver solutions that are safe and fit for the market. But then you need to gain market buy-in because, at the end of the day, we can have the solution but we need to get customers to buy in and source those solutions. Therefore, what we are doing in parallel is to build up strong fact-based literature on the safety and the impact of our products. For example, last year we asked a third-party university and research institute to assess the safety and the sustainable impact of our recycled PET. The results were amazing in terms of safety and from the Life Cycle Assessment too.
The tests confirmed that we are offering a sustainable solution that is similar in terms of processability and performance to a virgin product.
As a second part of the investigation, we asked a third-party agency to evaluate the lifecycle of our product and the life cycle assessment impact came out at 37% less.
Being able to produce and market a product that is coming from recycled materials, that has a positive impact in terms of reduced energy consumption and waste, and one that uses renewable resources, I think, is an amazing result.
We are also introducing a chemically recycled material right now too. Chemical recycling offers the possibility to transform the polymer back into a monomer and then the monomer back to a polymer, ending up with a safe and clean plastic totally comparable with a virgin material. This process opens up to the post-consumer collection and usage of a much larger volume of materials, increasing tremendously the possibility to offer recycled materials to a larger audience of customers.
As per Bormioli Pharma’s brand idea, “small parts with a big impact”, we want our impact to grow bigger and bigger, step by step, and continuously.
Which areas will pose the most challenges and what do you think these will be?
The technological aspect is very challenging, and this is without any doubt the most difficult goal to be achieved for our technicians, scientists, material experts, and others involved in the project. They are working daily and very hard in order to meet those targets. Of course, building up a solid and reliable supply chain is fundamental to be the selected as preferred partner for the pharmaceutical industry. However, the most challenging phase of the project is to convince the industry of the safety and reliability of the solutions we are offering. This is why we are investing heavily not just on technology, but also on gathering data and building literature, on building knowledge, and on spreading expertise.
We are speaking about medicine. We are speaking about drugs, something that is having a direct impact on people’s lives. It’s very important to have solid and scientific-based evidence of the results, and secure that all we are promising is fitting and complies with all the regulations.
Do you think that other pharmaceutical packaging companies should be setting similar goals and how achievable would this be on a more industry-wide basis?
As a person living on this planet, I hope that everybody will successfully enter into similar programs, I would hope that all that Bormioli Pharma has built up across almost 20 years of sustainability efforts will still put us a little bit ahead of the competition, challenging everyone to get similar achievements at short notice. Saying that, I'm expecting that everybody will follow, this is the path of evolution. I think that's part of the commitment of any company working in the medical care industry. We should be able to save life or to preserve life, but it is mandatory to preserve also the environment where those people are living.
How can government bodies and other pharmaceutical sectors such as suppliers work with the packaging industry to make a positive impact on the environment?
I think there are different opportunities to strengthen the process. For sure, the pharmaceutical industry should commit on that direction too, because they are the end user. We cannot force customers to use our sustainable solution unless they want to. But I have to say that in recent years the industry is strongly pushing in that direction. The pharmaceutical industry is really committed to making a strong impact here.
In terms of sustainability, of course we need to increase the numbers of suppliers able to provide pharma-grade products in large quantities because if we want to have a real impact, we need to have that initially in the volumes and quantities we can provide. But one of the most critical areas where we need to enact change is in regulatory.
We are currently working with some other companies to lobby the regulators on some policies. For example glass; why not reuse the glass already used for pharmaceutical applications as the glass will be melted again at 1600 °C and the science shows us that any kind of impurity is completely destroyed by the heat, so why not change the law and give the possibility to companies like Bormioli to reuse 100% of the products they’ve produced and shipped to the end users? We are already working on the feasibility of a project to collect products from hospitals, from healthcare systems, and to recycle it, but that's not yet possible by law.
Even in terms of plastic, sometimes it is not the matter of technical features but a matter of regulatory features. So sometimes we are obliged not to move forward even if there are the possibilities to do so. Chemical recycling offers a huge amount of possibilities, but right now is limited only to specific applications.
I can’t say everything will be made available, but based on scientific evidence we should be able to recycle more products. We know there is a concern over products going through the medical supply chain but, we have already developed a serialisation concept, based on a cutting-edge laser technology, for our containers and this serialisation not only offers huge benefits in terms of combating counterfeiting in the supply chain but opens the industry to innovative collection and recycling systems.
It is a great solution for supply chain control, but it can also offer the possibility to implement a very specific and targeted recycling system. If you have a unique barcode or a QR code, then you can scan it and you know from where that particular product comes from, you can get info on the type of glass and even on the Bormioli plant in which it has been produced. Then you can collect the product through a specific re-collection system and then it gets back to the same plant in which it was produced initially.
I personally believe in a solid circular economy business model, but right now what prevents us are not always technology constraints. In multiple cases the limits are set at the legislative level. We are keen to take sustainability and circular economy to the next level and to improve the mine of tools and solutions we have at our disposal, making our sustainable primary packaging solutions accessible to a wider audience, and in that way having a bigger impact on limiting climate change.
Related News
-
News Pharmapack Awards 2024 Patient-Centric Design Award Winner – Dr Ferrer BioPharma
The 2024 Pharmapack Awards celebrated the best in innovation and design for the pharmaceutical packaging and drug delivery industry on January 24, 2024. -
News Pharmapack 2024 - From the Floor
Paris once again welcomes Europe’s leading trade show in pharmaceutical packaging and drug delivery innovation. Join our content team as Pharmapack 2024 opens its doors to leading experts and innovators in pharmaceutical packaging and drug delive... -
News On Track at Pharmapack 2024 - The Track Sponsor interview: BD Pharmaceuticals
January 2024 brings both a new year and Europe’s leading packaging and drug delivery event. Bringing the world’s experts in pharmaceutical packaging together in Paris, France, Pharmapack 2024 brings exciting opportunities to learn and colla... -
News CPHI Pharma Awards 2023 – API Development and Innovation Winners: Snapdragon Chemistry, a Cambrex Company
After another year of impressive nominations for the CPHI Pharma Awards our winners were announced at CPHI Barcelona in October. In this series of interviews, we speak to the teams behind the award-winning projects, concepts, and technologies. -
News PharmaKure gains authorisation for next stage testing on Alzheimer's treatment
Clinical stage pharmaceutical company PharmaKure gains permission from UK authorities to enter into further testing for PK051 for the treatment of patients with mild cognitive impairment associated with Alzheimer's disease. -
News New Novo Nordisk AI hub for drug discovery to open in London, UK
Danish pharmaceutical giant Novo Nordisk will be opening an AI-based research facility in the heart of London to advance drug discovery operations. -
News Navigating the Future: Challenges and Opportunities in Pharma Innovation and Investment – CPHI Barcelona 2023 Roundtable Report
In this comprehensive downloadable report, hear from a range of experts in finance and investment in the pharma industry on what investment trends will be shaping the future of the industry, in Catalonia, and the wider world. -
News BioNTech to begin mRNA vaccine manufacturing in Rwanda by 2025
German biotechnology company BioNTech has stated their intentions to begin production at their mRNA vaccine factory in Rwanda by 2025, which will mark the first foreign mRNA vaccine manufacturing site on the continent of Africa.
Position your company at the heart of the global Pharma industry with a CPHI Online membership
-
Your products and solutions visible to thousands of visitors within the largest Pharma marketplace
-
Generate high-quality, engaged leads for your business, all year round
-
Promote your business as the industry’s thought-leader by hosting your reports, brochures and videos within your profile
-
Your company’s profile boosted at all participating CPHI events
-
An easy-to-use platform with a detailed dashboard showing your leads and performance