CPHI Pharma Awards 2023 – API Development and Innovation Winners: Snapdragon Chemistry, a Cambrex Company
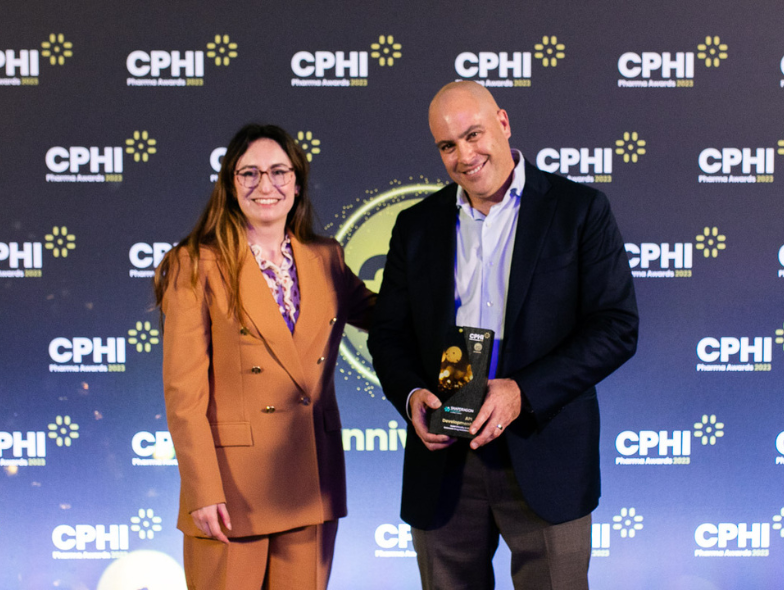
After another year of impressive nominations for the CPHI Pharma Awards our winners were announced at CPHI Barcelona in October. In this series of interviews, we speak to the teams behind the award-winning projects, concepts, and technologies.
The winner for the API Development and Innovation was Snapdragon Chemistry, of Cambrex, for their innovative process development of a continous flow-manufacturing system, which helps to recycle unwanted elements in the pathway to developing new therapeutics. In this interview Matthew Bio, Chief Scientific Officer of Cambrex and President of Snapdragon Chemistry, tells us more.
Please can you give some background to Snapdragon Chemistry and the aims and goals of the company?
Snapdragon Chemistry, a Cambrex company, was founded with a focus to provide expertise in continuous manufacturing technology to pharmaceutical and fine chemical industries. As part of that effort, we have developed technologies for data-rich process development workflows, process automation, at-line & in-line PAT tools, and novel reactors for flow chemistry.
In recent years, we have leveraged our process development capabilities, in collaboration with drug innovators, to develop and manufacture new, complex synthetic therapeutic modalities. Throughout the company’s history, our core mission has been to leverage deep process understanding for the goal of developing improved chemical processes. The continually increasing complexity of synthetic therapeutic agents demands a comprehensive understanding of the chemistry and processes required to deliver these novel medicines to clinic and patients.
You won the ‘API Development and Innovation’ prize for your continuous flow-manufacturing system – please can you tell us a little more about this project?
The innovator partner came to Snapdragon with the goal of developing a process to recycle the undesired atropisomer of a complex intermediate en route to an important new oncology therapeutic. The atropisomer has an exceptionally high barrier to rotation and required extreme conditions to convert the undesired enantiomer to a racemic mixture that could be recycled through the process. The recycling of the intermediate enabled a much greener process through the salvage of the undesired enantiomer as recognised with an EPA Green Chemistry Challenge award in 2022. Our collaboration resulted in the peer-reviewed scientific publication Org. Process Res. Dev. 2022, 26, 2636-2645.
What challenges have you encountered in developing the process and how did you overcome these?
The primary challenge was to figure out a way to safely operate a process that required the extreme conditions of ~300 °C and 32 bar pressure. Our process safety engineers studied potential failure modes and operating challenges to determine the potential hazards. It was first necessary to confirm the stability of substrate and product to the high temperatures required.
Next, to support operation in a plug flow reactor, we had to identify a solvent that was both stable at the high temperature and able to solubilise both starting material and product at the start and finish of the reaction. The extreme temperature meant that some degree of degradation of solvent, reactant, and product was inevitable, so balancing the productiveness of the process against degradation was a significant focus of development.
To address these challenges, we were able to develop scale-down models of the process that allowed us to evaluate the reaction kinetics and rapidly assess different conditions. As we iterated on the process conditions it was important to revisit the process safety assessment to ensure that we were able to maintain safe operating windows. As we settled on a reactor design, based on the scale-down model, each possible failure mode was considered and extrapolated to the worst case scenario and then a mitigation strategy was developed.
To demonstrate the process, construction of a pilot scale reactor at 1/10 commercial was undertaken. We were able to leverage years of experience with reactor design and automation to quickly develop a pilot reactor representative of the planned commercial system and demonstrate the process.
The continuous flow-manufacturing process development represents a big step in API manufacturing, how will this revolutionise manufacturing in becoming more sustainable?
In the case of the atropisomer recycling, the sustainability gains obtained through recycling of the undesired enantiomer are only practical using continuous technology. The high temperature and pressure required for the reaction make batch processing to recycle impractical. More broadly, there are a number of ways in which continuous technology can improve the sustainability of processes.
For reactions that are high or low temperature, the high heat transfer efficiency of flow reactors combined with heat recovery can significantly lower utility requirements. In batch reactions, we often rely on a large volume of solvent just to manage the heat generated by exothermic reactions. By utilising flow reactors with high efficiency heat transfer, we can reduce or eliminate the need for solvent and still safely manage the heat, resulting in significant intensification. Even where large volumes of solvent are required for the reaction, connection of the flow systems to solvent recycle can also accomplish process intensification.
More interesting is the use of flow technology to enable new methodologies for molecule construction. Chemical technologies such as (hetero)arene metalation, photoredox, and electrochemical transformations can offer highly efficient routes to APIs. But in many cases these technologies are challenging, if not impossible, to execute at commercial scale in batch so alternative, less efficient routes of constructing API are selected. With continuous flow processing, these methodologies can be practically executed at the scale required to support commercial demand.
How will this technology be used to help with regulatory compliance?
Continuous flow manufacturing often provides a great deal of data about the control over a process in real-time. Factors like pressure, temperature, and feed rates, are constantly monitored and maintained within target control ranges. With a well understood process, control of these process variables typically translates to consistent product output with the target quality attributes.
If something changes outside of proven acceptable ranges, the deviation is quickly recognised and automated diversion of product can be used to ensure out of specification material does not end up in the product. Control over other factors that may be critical to product quality, such as mixing rate, heat transfer rate, and residence time, can be ensured by the design of the equipment itself. These properties of continuous processes and reactors greatly simplify the control over product quality.
What does winning the award mean to you and how will it help you as a company?
I was honoured to represent the team behind the work and it is a great accomplishment for our company to have been recognised at CPHI, such a major event for our industry. Despite a long history of the use of continuous manufacturing in pharmaceutical manufacture, there is still the impression that flow is a novel technology and challenging to use.
An award like this highlights the utility of continuous technology to address pharmaceutical manufacturing challenges and normalises the technology. It is our hope, at Snapdragon, that the industry recognises flow technology as just another tool for pharmaceutical manufacturing, and one that can provide significant advantages in the right situations.
What does the future hold for Snapdragon Chemistry? What projects do you have in the pipeline?
A major focus for the last few years has been the development of new tools to facilitate process development. We recently introduced a sample relay system (SRSTM) to enable at-line U(H)PLC analysis of batch and flow processes. With the ability to analyse in near real time, we have been able to deploy optimisation algorithms for process optimisation and automate DoE projects to accelerate process design, development, and characterisation activities. The next step is to leverage the rich data sets available from these automated workflows as training sets in machine learning applications for the development of predictive models.
At the same time, we have leveraged our tools and expertise for the development and manufacture of complex synthetic API modalities like peptides, oligonucleotides and other synthetic polymers used in therapeutic applications. We are using capabilities in membrane purification technologies and automation to design improved methods for manufacturing these complex synthetics and supporting the development of novel modalities as human therapeutics.
About Matthew M Bio
Matthew Bio is the Chief Scientific Officer of Cambrex and President of Snapdragon Chemistry, a Cambrex Company. Matthew began his career in chemistry 30 years ago developing continuous processes for the manufacture and purification of acrylates at the former Rohm & Haas company. Matthew then moved to Columbia University and earned a PhD in Chemistry. Upon graduating, Matthew returned to industry as a process development chemist at Merck Research Laboratories. In 2006 Matthew moved to Amgen where he worked on the development of both batch and continuous manufacturing solutions for synthetic drug substances. He also worked on the development of new manufacturing technologies for synthetic – biologic hybrid molecules. In 2015, Matthew became a founding member of Snapdragon Chemistry, Inc., a contract development firm specialising in chemical process development and continuous manufacturing technology.
Related News
-
News CPHI Pharma Awards 2023 – Supply Chain Excellence Winners: Catalent Case Management Services
After another year of impressive nominations for the CPHI Pharma Awards our winners were announced at CPHI Barcelona in October. In this series of interviews, we speak to the people and teams behind the award-winning projects, concepts, and technologie... -
News Navigating the Future: Challenges and Opportunities in Pharma Innovation and Investment – CPHI Barcelona 2023 Roundtable Report
In this comprehensive downloadable report, hear from a range of experts in finance and investment in the pharma industry on what investment trends will be shaping the future of the industry, in Catalonia, and the wider world. -
News CPHI Barcelona 2023: Partnering for Success – Managing Outsourcing Relationships to Optimise Manufacturing Operations
During CPHI Barcelona 2023, insightful content sessions offered attendees the chance to explore trending topics with expert speakers and panellists. Here, we summarise what the pharma industry and supply chain are talking about the most. -
News CPHI Podcast Series: The 2023 Retro – what have we learnt from the past year in pharma?
Welcome to the last episode of 2023! Digital Editor Lucy Chard is joined by her teammates in a special retrospective episode to close out the year. Guests Vivian Xie, Editor for CPHI Online and Tara Dougal, Content Director for Pharma, discuss their hi... -
News CPHI Pharma Awards 2023 – Accelerating Innovation Winners: React4Life
After another year of impressive nominations for the CPHI Pharma Awards our winners were announced at CPHI Barcelona in October. In this series of interviews, we speak to the teams behind the award-winning projects, concepts, and technologies. -
News CPHI Pharma Awards 2023 – Regulatory & Compliance Winners: Lambda Therapeutic Research Ltd.
After another year of impressive nominations for the CPHI Pharma Awards our winners were announced at CPHI Barcelona in October. In this series of interviews, we speak to the teams behind the award-winning projects, concepts, and technologies. -
News CPHI Barcelona 2023: Loading Potential – Artificial Intelligence for Pharma Manufacturing
During CPHI Barcelona 2023, insightful content sessions offered attendees the chance to explore trending topics with expert speakers and panellists. Here, we summarise what the pharma industry and supply chain are talking about the most. -
News CPHI Podcast Series: Start-ups take centre stage at CPHI Barcelona
The first episode of the CPHI Podcast Series since we attended CPHI Barcelona in October covers the Start-up market at the event, with expert Matthew Wise joining Editor Lucy Chard to discuss the event.
Position your company at the heart of the global Pharma industry with a CPHI Online membership
-
Your products and solutions visible to thousands of visitors within the largest Pharma marketplace
-
Generate high-quality, engaged leads for your business, all year round
-
Promote your business as the industry’s thought-leader by hosting your reports, brochures and videos within your profile
-
Your company’s profile boosted at all participating CPHI events
-
An easy-to-use platform with a detailed dashboard showing your leads and performance