Sterile manufacturing Annex 1 amendments: what, why and how explained
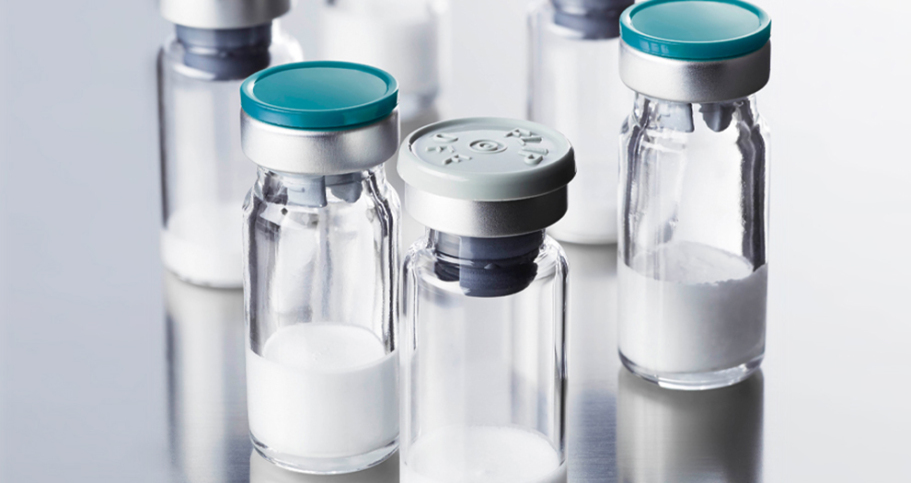
In January 2020 the European Commission published some proposed significant revisions to Annex 1, the EU’s good manufacturing practice (GMP) guide for the manufacture of sterile products. In the following three-month consultation period, affected organisations and stakeholders from over 70 different countries submitted more than 2,000 comments to the proposed update.
In this article Dr. Thomas Becker, Director Quality at Recipharm in Wasserburg, discusses the key changes to the guide and the impact it will have on companies responsible for the manufacture of sterile products as the industry continues to work to meet the industry’s changing requirements and overcome reoccurring challenges in the supply chain.
The changes saw the scope of Annex 1 enlarged to include guidance to non-sterile product manufacturers, where contamination control is relevant, and its format was reorganised into 10 distinct sections. Beyond this, the main changes include:
- Introduction of a contamination control strategy (CCS) concept, quality risk management (QRM) principles and a pharmaceutical quality system (PQS).
- Additional QRM principles included to support non-sterile product category.
- Introduction of restricted access barrier systems (RABS) and isolators, as well as some additional new technologies as part of the CCS requirements.
- The creation of new sections for form fill and seal, closed systems, and single use systems (SUS).
- Reinforced recommendations for area classification and qualification, including microbial airborne and surface contamination.
- The introduction of detailed measures and specifications to prevent any contamination (for example, unidirectional material flow, continuous monitoring systems for total organic carbon and conductivity on water for injection loops, validated disinfection and decontamination programme including a focus on vacuum, cooling systems, and dry heat tunnels).
- The introduction of specific personnel requirements, including training and gowning, combined with reinforced monitoring requirements.
- Stipulations about production and the use of specific technologies including, pre-use post sterilisation integrity tests (PUPSIT), specific process holding times, container closure integrity, and visual inspection.
- Mandatory reinforced sterility test sampling after each critical intervention.
- Additional aseptic process simulation runs before shut down periods are to be taken into consideration.
- Trending dating for environmental monitoring and visual inspection results are to be taken into consideration for batch release.
Overall, these new additions to the guidelines could potentially pose significant challenges to pharma companies both technically and organisationally; Key examples would be updating equipment or premises design to minimise contamination risk, integrating new equipment, such as barrier technologies, into a CCS containing older systems using QRM principles, ensuring an approach that guarantees regular reviews of each risk assessment and the review of data and trends generated by critical CCS equipment.
That being said, successfully implementing these new rules could bring about improved safety and anti-contamination measures. In addition, the growing involvement of other regulatory organisations and stakeholders such as the International Pharmaceutical Inspection Convention and Pharmaceutical Inspection Co-operation Scheme (PIC/S), the World Health Organisation (WHO) and the US Food and Drug Administration (FDA) could mean harmonised compliance requirements across the global market.
At Recipharm we have worked to successfully implement the required measures to ensure continued compliance during the manufacture and handling of sterile and non-sterile products requiring contamination control. By taking a proactive approach to meeting the changing demands of Annex 1 we will be able to continue to provide seamless sterile project solutions for out customers.
For more information on how the updates to Annex 1 will affect your operations, guidance on how to meet the new requirements or more information about our sterile manufacturing offering please contact Recipharm’s expert team here.
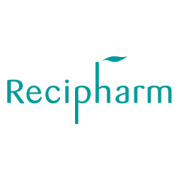
Related News
-
News Pharmapack Awards 2024 Patient-Centric Design Award Winner – Dr Ferrer BioPharma
The 2024 Pharmapack Awards celebrated the best in innovation and design for the pharmaceutical packaging and drug delivery industry on January 24, 2024. -
News Pharmapack Awards 2024 - Celebrating Packaging and Drug Delivery Innovation
The 2024 Pharmapack Innovation Awards ceremony celebrated the best in pharmaceutical packaging and drug delivery innovation at all levels. The awards were held on January 24, 2024 at the Paris Expo Porte de Versailles. -
News Women in Pharma: Looking back on 2023 and moving forward to 2024
In this monthly series, we interview women from across the pharmaceutical industry and supply chain to discuss the importance of gender diversity in healthcare, the workplace, and beyond. -
News On track at CPHI Barcelona - The Track Sponsor interview: USP
In our packed out content sessions at CPHI Barcelona this year we focus on some of the hottest topics coming up in the pharma industry, with each track sponsored by a leading expert in the field. -
News Women in Pharma: Marketing for the other half in healthcare
In our new monthly series, we interview women from across the pharmaceutical industry and supply chain to discuss the importance of gender diversity in healthcare, the workplace, and beyond. This instalment highlights not only the importance of ma... -
News Bringing the pharmaceutical supply chain closer to home
The pharmaceutical supply chain has encountered numerous disruptions in the last few years, impacting procurement, manufacturing, packaging, and distribution operations within the pharmaceutical industry. Read about the rise in calls for near/resh... -
News Delivering on mRNA-based therapeutics: innovations in applications and packaging
Since the onset of the COVID-19 pandemic, the innovative potential of mRNA vaccines and therapeutics has raised questions regarding their manufacturing, packaging, and storage/transportation. Learn about how the pharmaceutical supply chain is meet... -
News Your Prescription for Marketing Success: Digital Pharma Marketing Toolkit – Free eBook
Download your FREE pharma marketing eBook to learn why it is so important for pharmaceutical marketeers to develop their digital content marketing strategies in order to establish their companies as thought leaders and industry experts.
Position your company at the heart of the global Pharma industry with a CPHI Online membership
-
Your products and solutions visible to thousands of visitors within the largest Pharma marketplace
-
Generate high-quality, engaged leads for your business, all year round
-
Promote your business as the industry’s thought-leader by hosting your reports, brochures and videos within your profile
-
Your company’s profile boosted at all participating CPHI events
-
An easy-to-use platform with a detailed dashboard showing your leads and performance