FPS Food and Pharma Systems S.r.l.
About FPS Food and Pharma Systems S.r.l.
Certifications
Categories
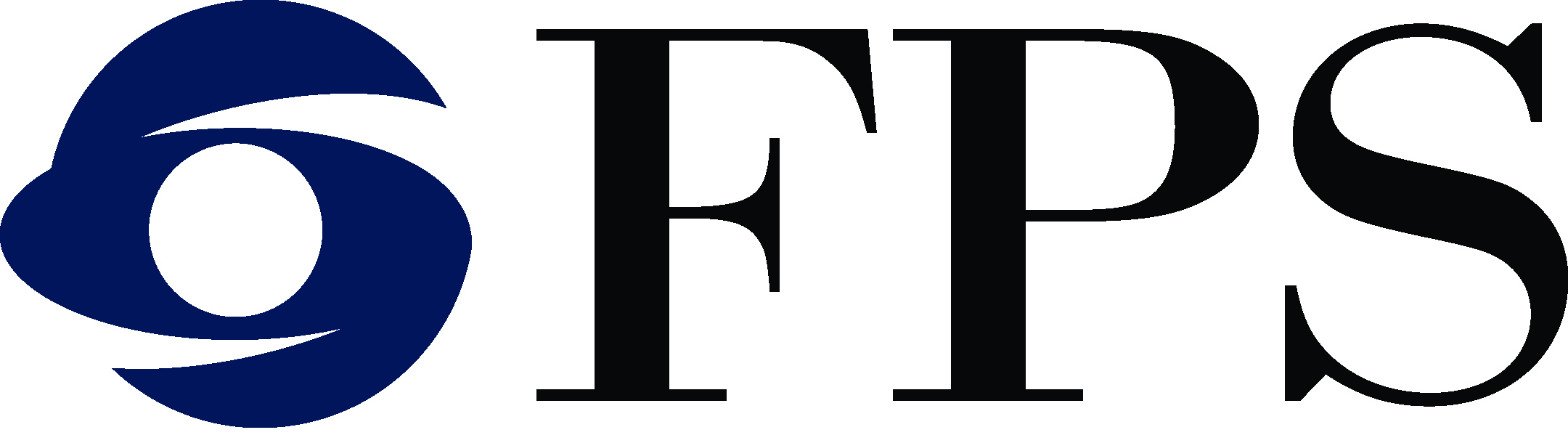
-
IT
-
2015On CPHI since
-
3Certificates
-
50 - 99Employees
Company types
Primary activities
Meet us at
CPHI Milan 2024
Fiera Milano, Italy
08 Oct 2024 - 10 Oct 2024
Products from FPS Food and Pharma Systems S.r.l. (5)
-
Product Isolators for High Potency API Containment: Toxic Applications
FPS custom isolators are meticulously engineered to meet every requirement and to safeguard operators, products, and environments in toxic pharmaceutical applications. Crafted from robust stainless steel, they offer unparalleled protection during micronization and beyond. Transparent acrylic parts can also... -
Product Aseptic Isolators for Sterile Applications
FPS sterile containment systems maintain a sterile environment around processes, requiring minimal space and eliminating the necessity for sterile cleanrooms. Our custom isolators are meticulously engineered to meet the highest pharmaceutical standards, ensuring impeccable sterile condi... -
Product High Containment isolator for Micronization
The latest challenge was to design a multi-purpose isolator used to micronize down to a few microns covering a wide range of batch size and assuring a Containment Performance Target (CPT) of 50ng/m3. Inside the isolator, a 4”, 8” or 12” jet mill can be used. To achieve this, a 9-chamber isolator has been d... -
Product Sterile isolator for PilotMill-6
Benefits of FPS Solution:
• FPS provides both the containment system and the micronization unit • All components of the micronization units are designed to be connected to the Sterilization In Place line • Decontamination cycles specifically developed to guarantee an aseptic environment... -
Product Toxic Sterile Dispensing Isolator
FPS has recently designed and manufactured an isolator designed to introduce up to 100kg of potent sterile API and dispense it in specific containers to be connected to the process equipment. During the initial phase of listening to the customer’s needs, the different stages of the process were analyzed...
FPS Food and Pharma Systems S.r.l. Resources (2)
-
News Laminar flow booths
High level of air quality in a confined space -
Video Stefano Butti, FPS Head of the Sales Group, talks about the current italian market situation, what FPS expects from the future and other company news
Today we’re here to talk about the just passed year and how it was for FPS especially for the Italian Market.
First of all, I’d like to underline that we’re very proud to be Italian and we’re proud how the Italian Market response about the current situation of Covid 19. As we always mentioned on our social profile, FPS has never stopped and we always given ...
Position your company at the heart of the global Pharma industry with a CPHI Online membership
-
Your products and solutions visible to thousands of visitors within the largest Pharma marketplace
-
Generate high-quality, engaged leads for your business, all year round
-
Promote your business as the industry’s thought-leader by hosting your reports, brochures and videos within your profile
-
Your company’s profile boosted at all participating CPHI events
-
An easy-to-use platform with a detailed dashboard showing your leads and performance