Microinnova Engineering GmbH
About Microinnova Engineering GmbH
Certifications
Categories
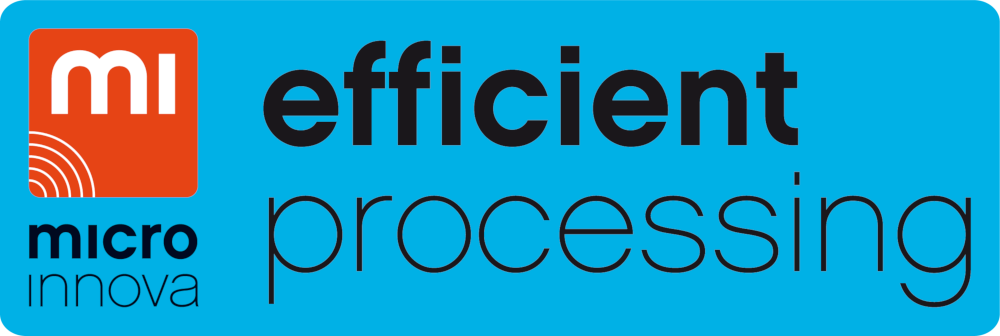
-
AT
-
2015On CPHI since
-
5Certificates
-
25 - 49Employees
Company types
Primary activities
Products from Microinnova Engineering GmbH (8)
-
Product Continuous Manufacturing API Plant
Continuous Manufacturing API Plant -
Product Engineering Services for Continuous Manufacturing and for Modular Plants
Basic Engineering - Transform your optimized process into manufacturingMICROINNOVA's engineering team is turning developed continuous chemical laboratory processes into your desired manufacturing plants. Starting with first steps such as piping and instrumentation diagrams (P&ID) and a U... -
Product Flow Miniplant
Bench-top pilot plant for development and small-scale production. The Flow Miniplant is Microinnova’s bench-top flow pilot-plant for the production of quantities between 1 and 100 litres per hour. It bridges the gap between lab-scale flow process development and bulk manufacturing. It’s an indispensable st... -
Product GMP Modular Continuos Manufacturing API Plant with Solids
We specialize in process development and the design of modular plants and have developed an excellent concept for it. We provide the whole package. From process design, over cost evaluation, to your turnkey plant, optimized and tailored to suit your specific needs. The implementation of a modular... -
Product Modular Continuous Manufacturing Crystallization Plant
Modular multi-purpose API crytallization plant with PAT and module predictive control. -
Product Overview Products and Services Continuous Manufacturing
PROCESS RESEARCH
Development of efficient synthesis routes using the advantages of continuous processing.
PROCESS DESIGN
Decades of experience in process intensification, flow chemistry and continuous processing gives us the ability to investigate the best appro... -
Product Plant Debottlenecking by Continuous Manufacturing Case Study
Debottlenecking through Continuous Production Capacity increase by means of small skids in the batch plantContinuous production will help you solve the bottlenecks you are currently facing with batch production. The advantages of continuous production are countless, but we have summarized an... -
Product Continuous Manufacturing of Formulations in Minutes Instead of Hours
Microinnova Engineering GmbH has successfully commissioned two continuous formulation production plants for a European client. The design of the fully automated plant is very compact, which makes it possible to easily transport & install it at a different manufacturing site on the other side of the wor...
Microinnova Engineering GmbH Resources (10)
-
Sponsored Content Capacity Boost by Batch-to-Conti Debottlenecking
Space economy is a typical issue for debottlenecking projects. Since a continuous approach reduces mass and heat transfer distances up to a factor of 100, these solutions can easily be integrated into an existing batch environment.
-
Brochure Who is Microinnova?
A short presentation highlighting our expertise! -
Sponsored Content Modular Plants: Speed as the Key Success Factor for Chemical Businesses in the Future
We expect that speed and flexibility will be success factors for chemical businesses in the future.
-
Brochure Microinnova Chemistry Portfolio
PROCESS RESEARCH
Development of efficient synthesis routes using the advantages of continuous processing.
PROCESS DESIGN
Decades of experience in process intensification, flow chemistry and continuous processing gives us the ability to investigate the best approach and strategy to put your process into an efficient system.
CHEMICAL AND TECHNICAL FEASIBILITY
Inside our flow lab scale plants we have multiple technologies available to develop continuous experimental procedures with the principal objective of showing a reliable mode of operation.
OPTIMIZATION & PILOT PHASE
Depending on the inherent characteristics each verified continuous process is optimized. The optimal processing window is determined on scalable equipment to finally deliver a robust continuous system.
-
Sponsored Content Corning and Microinnova Celebrate Opening of Advanced-Flow™ Reactor Qualified Lab
Corning Incorporated and Microinnova recently celebrated the opening of the Corning® Advanced-Flow™ Reactors (AFR) Application Qualified Lab (AQL) at their facility near Graz. Application qualified labs enable AFR customers to effectively access continuous-flow demonstrations, experimental trials, feasibility testing, and chemical reaction process development.
-
Video Modular Plants for Smart Manufacturing
My name is Katharina and I will show you how continuous modular plants will change chemical processing for a more sustainable future, using modular plug & play plants. We see some issues with batch processing. Sometimes there are concentration spots, the walls are too hot for the molecules. Our philosophy is that all molecules should have the same processing conditions. This we realize by looking at the critical parameters of the chemistry and selecting the right process intensification technology. Furthermore, the space-time-yield can be maximized by a magnitude or more by reducing mass and heat transfer distances, leading to much shorter residence times and compact designs. Since we already have a continuous operating plant in the lab, scale-up becomes much easier. Continuous manufacturing allows for superior quality control due to advanced PAT. Standardized modules enable a quick realization of reduced time to produce and time-to-market. More infos below video! -
Sponsored Content Intensification Boost for Enzymatic Liquid/Gas Processes by means of Continuous Flow Processing
O2-dependent biotransformation reactions have proven difficult in fine chemical manufacturing due to the mass transfer limitations of supplying O2 to the enzymatic reaction, hence affecting the level of efficiency achieved.
-
Video 8 Differentiators that make Microinnova Unique
Microinnova serves its customers as a one-stop-shop from development to manufacturing plants. The following eight differentiators make Microinnova unique. 1. Microinnova focuses on end-to-end continuous manufacturing, dealing with processes in the area of synthesis, work-up and formulation.
2. We work with a wide range of different process intensification technologies. We select the best technology for each process. We want to enable uniform process conditions for each molecule.
3. We are used to working in regulated environments. We are DIN EN ISO 9001 certified. We can build plants that fulfill typical standards for regulated environments like GMP and ATEX.
4. We can handle various conditions. We can process highly viscous materials like melts, suspensions, precipitates and solids in packed or trickle beds.
Our other 4 differentiators you can find in the video! -
Sponsored Content Microinnova Sponsors Award for Outstanding Process Intensification Work Towards CO2 Reduction
We were honored to have the opportunity to sponsor the 2021 EFCE Excellence Award in Process Intensification.
-
Brochure 2nd Generation API Synthesis
Continuous Manufacturing with Half of the Unit Operations
Position your company at the heart of the global Pharma industry with a CPHI Online membership
-
Your products and solutions visible to thousands of visitors within the largest Pharma marketplace
-
Generate high-quality, engaged leads for your business, all year round
-
Promote your business as the industry’s thought-leader by hosting your reports, brochures and videos within your profile
-
Your company’s profile boosted at all participating CPHI events
-
An easy-to-use platform with a detailed dashboard showing your leads and performance